- christian2765
- Apr 13, 2023
- 1 min read
We are pleased to announce the completion of a new oak mullion, plant-on window at Orleton Manor, which has been carefully handcrafted by renowned cabinet maker, John Beavan. The process of creating this exquisite piece involved many hours of dedication and attention to detail.

John's passion for woodwork began at a young age of seven when he made a small table out of his mother's ironing board. Since then, he has honed his craft and is now considered one of the most accomplished and respected cabinet makers in the industry.
As a Sotheby's and Christies Listed Cabinet Maker with over 40 years of experience, John has worked with a diverse range of clients, from rockstars to royalty. His prestigious list of clientele is a testament to his skills and craftsmanship.
John's commitment to excellence is evident in the finished product. "Making something difficult - beautifully is what it's all about for me," he confirms. "I have a passion for perfection."
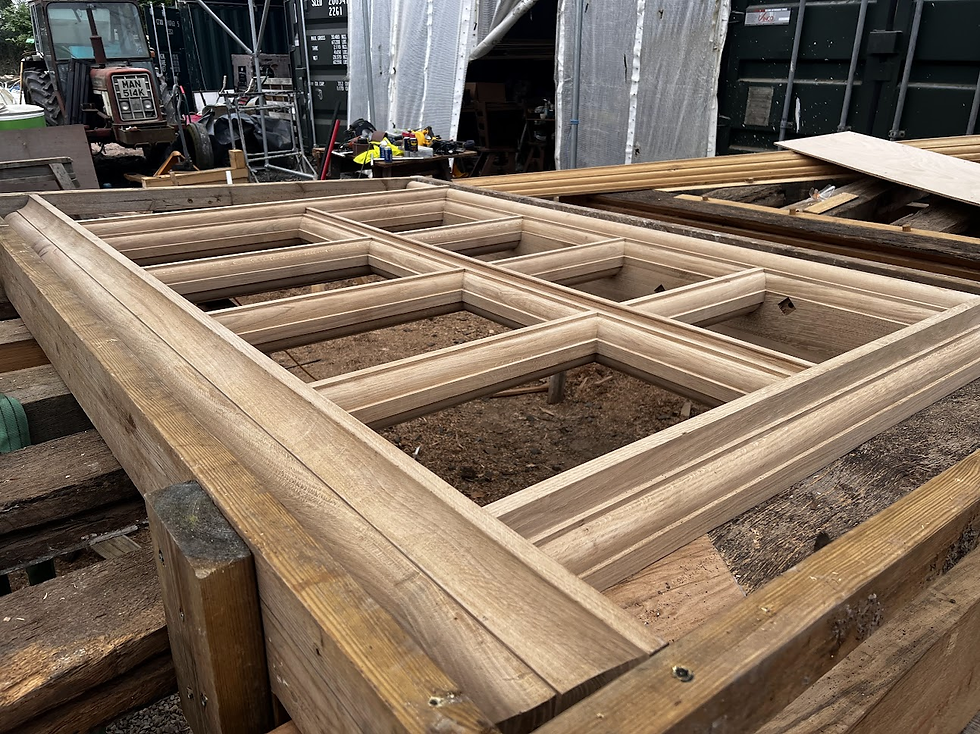
The completion of the oak window, which forms part of the structural timbers of the porch, is a proud moment for all involved. The intricate details and flawless finish are a testament to the dedication and skill of the joiner and his team. The window is not only functional but also a beautiful addition to the property's aesthetics.

In conclusion, the success of this part of the project is a testament to the importance of working with experienced and skilled craftsmen. John’s passion for perfection and dedication to his craft are reflected in this window, and we are delighted to have worked with him on this exceptional piece of joinery.
Exploded Repair Diagram by Montez Architecture
Gallery of additional Photographs